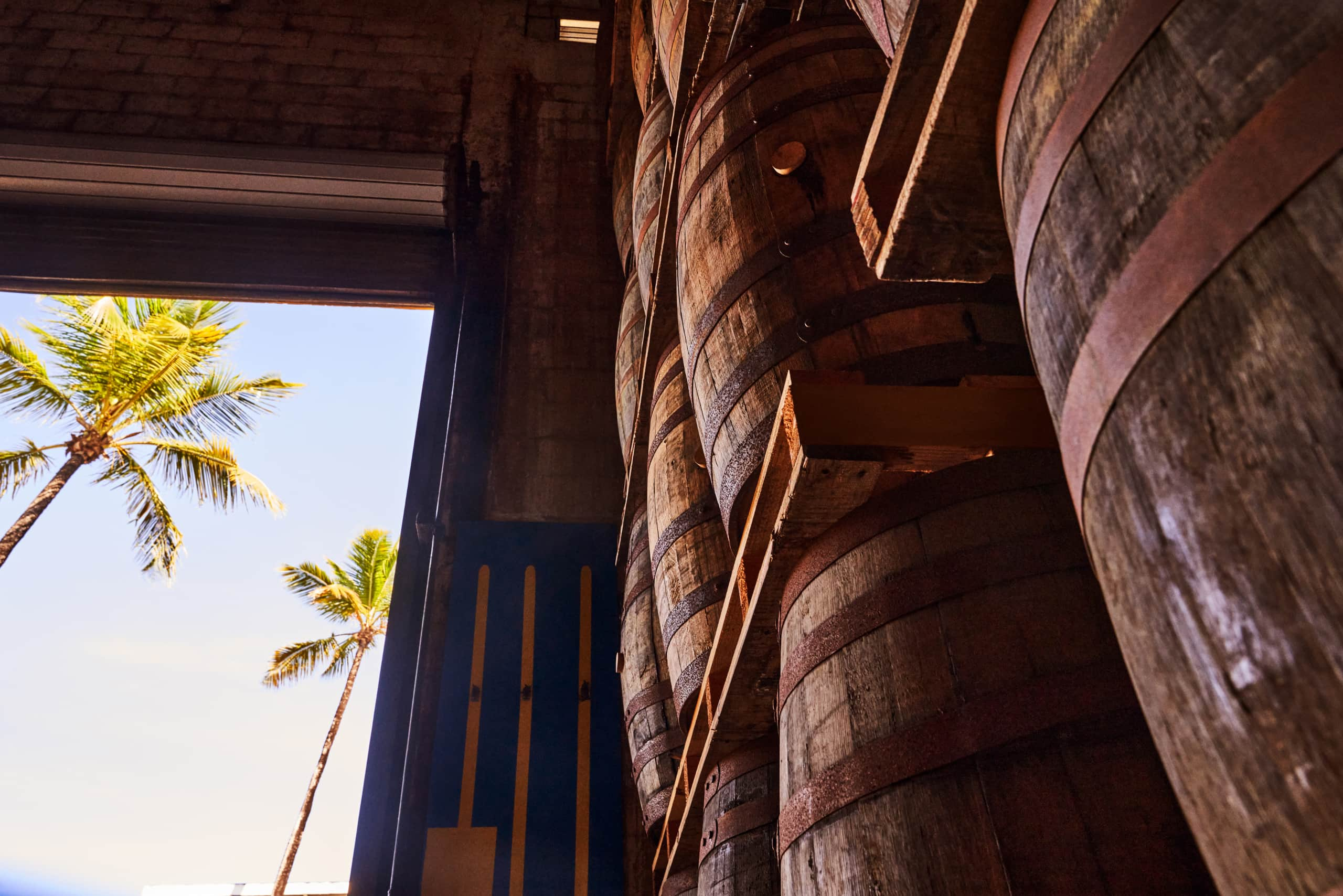
Corporate Sustainability
WE ARE GOOD SPIRITED
Making Moments Matter
At Bacardi, we take actions today to protect People & Planet for the future.
We are Good Spirited.
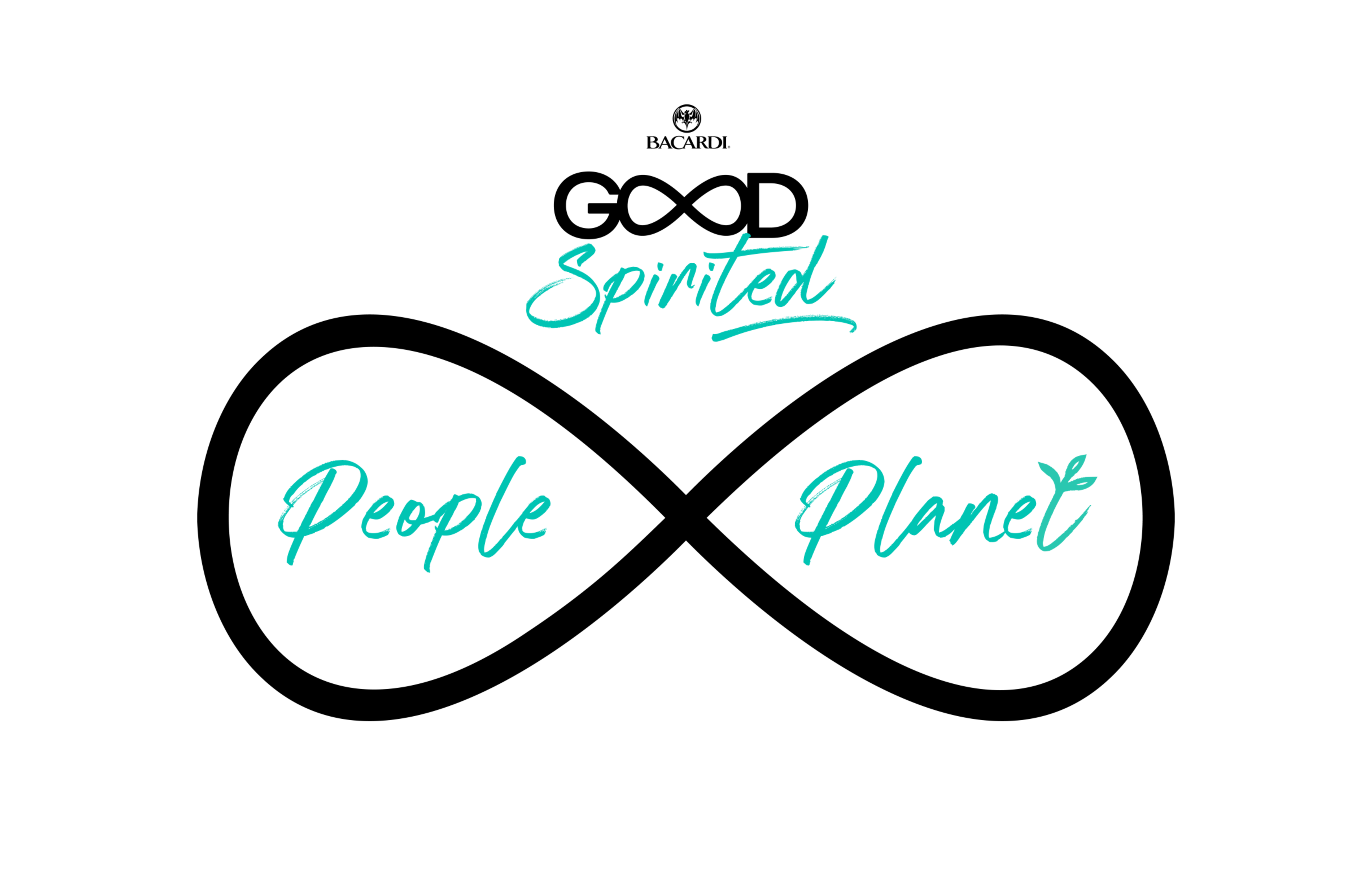
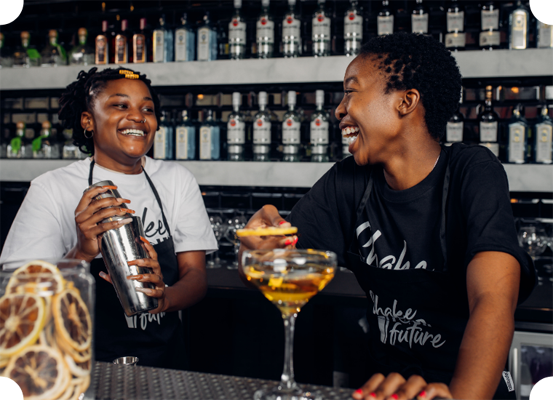
People
We care about people and invest in giving back to our communities.
We help drive employability in the communities around our sites and offices through our Shake Your Future and Build Your Future programs. We support the growers and farmers of our natural ingredients. We prioritize the safety of our teams and create an environment where everyone can be appreciated for who they are, what they do and who they can become.
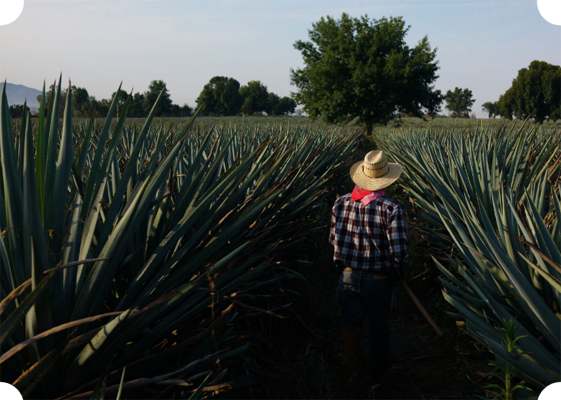
Planet
We prioritize reducing our impact on the environment.
We are taking real action today to reduce our greenhouse gas emissions and replenish water to protect this essential natural resource. We are focused on ensuring our packaging is reusable, recyclable or biodegradable. This is how we do the right thing.
Stories About Doing Good
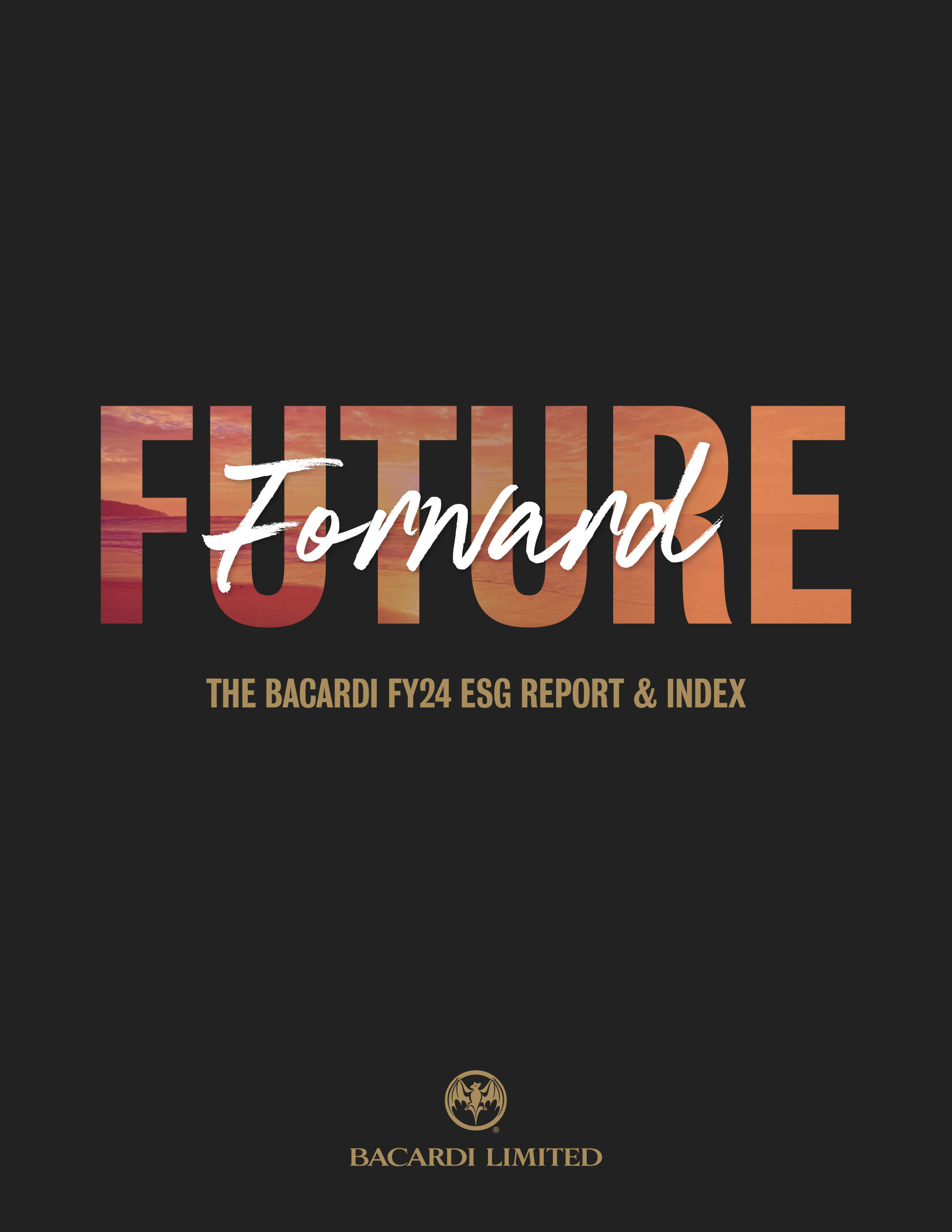